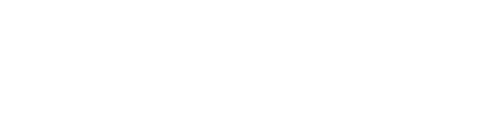
12,000 sq/m Manufacturing Facility
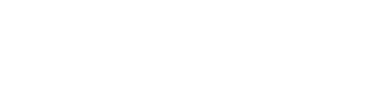
Experienced Engineers
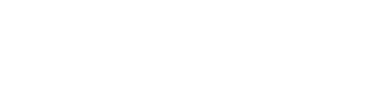
Up-to-date Machines

Satisfied customers
CNC Machining Service
Tight tolerances and finishing capabilities, as fast as 2 days.
Vacuum Casting Service
Production quality parts without the tooling investment.
Sheet Metal Fabrication
Experience the versatility 6 cost efficiency withflexible application options.
Die Casting Service
Create high quality custom mechanicals withprecision and accuracy.
Injection Molding Service
Production-grade steel tooling, as fast as weeks.
Carbon Fiber Manufacturing
Composite materials, such as carbon fiber reinforced plastics are highly versatile and efficiert materials.
Popular Services
Injection Molding Service
A faster, easier way to order high-quality injection molded parts that accelerates iteration, testing, and scaled production. Upload your designs for DFM feedback and pricing in 24 hours.
3D Printing Service
Our 3D printing solutions cater to personalised needs with a diverse range of materials and colour options, including SLA, SLS, FDM, Projet, DMLS, and MJF printing services.
Surface Finishing
The easiest way to source your custom parts, with 15+ surface finishing options.
Design Guide
In-depth design guides full of best practices for all of HLH's manufacturing processes.
Case Studies
Success stories from innovativecompanies using HLH.
Blog
lndustry trends, company news andproduct updates.
Featured Posts
Aerospace & UAV
HLH is your 3D manufacturing partner from prototype to large scale production.
Consumer Products
New Product Introduction Solutions for Consumer Products.
Automotive
New Product Introduction Solutions for Automotive.
Industrial Machinery
The main purpose of industrial prototyping is to take the product from drawings into the real world.
Robotics & Automation
Need some assistance bringing your robotic device or parts from the sketch-board to reality?
Medical Devices
The medical industry needs high quality, dependable and safe parts and products.
Communications
We understand the demands and ever changing landscape of the communications industry.
Product Development
Industrial design and engineering consultancies are some of the most innovate and creative enterprises on the planet.
HLH’s sheet metal solutions deliver the consistency, reliability, durability, and quality you expect from HLH, including material and finishing options to support your applications.
Bending
This manufacturing process uses dies to produce a U-shape, V-shape or channel shape along a straight axis in ductile materials.
Laser cutting
This manufacturing process uses a high-power laser beam to cut a material sheet.
Plasma Cutting
Plasma cutting is widely used in custom sheet metal services, it is especially suitable for custom cutting of thicker sheet metals.
Waterjet Cutting
Waterjet cutting is quite a different sheet metal service for its non-thermal feature. It is especially useful for cutting very thick metals, including steel.
12,000 sq/m Manufacturing Facility
Experienced Engineers
Up-to-date Machines
Satisfied customers
Sheet stock is procured in a flat state and cut then formed into its final state through a series of progressive steps. For a typical sheet metal project, the first step is equivalent to sheet cutting, where a shear, laser, waterjet, plasma, or punch press is used to create the internal holes and edge features of the part. This process is also known as blanking.
Once the blank is produced, the next step is to form sheet metal using various tools, but most commonly some sort of brake. A brake press can be manual or automated and uses die inserts to create a desired angular bend, forming the two-dimensional sheet into a three-dimensional object. Sheet metal forming can bend the part in multiple directions, creating simple parts such as brackets up to highly complex geometries which may require custom die tools. Once the tools are in place, making subsequent sheet parts in production is very cost-effective. This makes sheet metal fabrication and forming ideal for low to high volume production.
Stainless steel
Aluminum
Steel
Copper
Surface finishes can serve either a functional or aesthetic purpose. Surface finishes that serve both purposes are deemed cosmetic finishes, and are used for cosmetic parts. Producing cosmetic parts requires additional measures to minimize defects such as hang marks and scratches from tools.
√ Chromate Conversion
√ Nickel Plating
√ Anodizing
√ Powder Coating
Request a quote
Securely upload your part designs to our platform
Confirm specifications
Configure your part specifications and choose a delivery time that fits your schedule
Production
We select the best manufacturer for your order and start production immediately
QC
We take full responsibility for ensuring your parts are manufactured to our standards
Deliver goods
We handle all order logistics and communications, making sure your parts arrive on time.