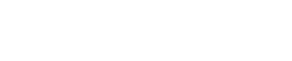
- info@prototypeshlh.com
- +86-133-9285-9203
- Room 2003, 20th Floor, Xingji Building, Shangde Road, Shajing Street, Bao'an District, Shenzhen
SERVICES
CNC Machining Service
Tight tolerances and finishing capabilities, as fast as 2 days.
Vacuum Casting Service
Production quality parts without the tooling investment.
Sheet Metal Fabrication
Experience the versatility 6 cost efficiency withflexible application options.
Die Casting Service
Create high quality custom mechanicals withprecision and accuracy.
Injection Molding Service
Production-grade steel tooling, as fast as weeks.
Popular Services
Injection Molding Service
A faster, easier way to order high-quality injection molded parts that accelerates iteration, testing, and scaled production. Upload your designs for DFM feedback and pricing in 24 hours.
3D Printing Service
Our 3D printing solutions cater to personalised needs with a diverse range of materials and colour options, including SLA, SLS, FDM, Projet, DMLS, and MJF printing services.
Surface Finishing
The easiest way to source your custom parts, with 15+ surface finishing options.
Design Guide
In-depth design guides full of best practices for all of HLH's manufacturing processes.
Case Studies
Success stories from innovativecompanies using HLH.
Blog
lndustry trends, company news andproduct updates.
Featured Posts
Aerospace & UAV
HLH is your 3D manufacturing partner from prototype to large scale production.
Consumer Products
New Product Introduction Solutions for Consumer Products.
Automotive
New Product Introduction Solutions for Automotive.
Industrial Machinery
The main purpose of industrial prototyping is to take the product from drawings into the real world.
Robotics & Automation
Need some assistance bringing your robotic device or parts from the sketch-board to reality?
Communications
We understand the demands and ever changing landscape of the communications industry.
Product Development
Industrial design and engineering consultancies are some of the most innovate and creative enterprises on the planet.
When it comes to manufacturing components, choosing the right production method is crucial for achieving the desired quality, efficiency, and cost-effectiveness. Aluminum alloy casting and CNC machining are two popular options, each with its own advantages and applications. Understanding the differences between these methods can help you make an informed decision based on your specific project requirements. Here’s a guide on how to choose between aluminum alloy casting and CNC machining.
(HLH CNC Machining Parts)
(HLH Aluminum Alloy Die Casting Parts)
1. Project Requirements
The first step in your decision-making process is to assess your project requirements. Consider the following factors:
Complexity: If your design features intricate shapes or internal cavities, aluminum alloy casting may be the better choice. Casting can easily produce complex geometries that would be challenging to achieve with CNC machining.
Tolerances: CNC machining excels in producing components with tight tolerances and high precision. If your project requires exact specifications, CNC machining is likely the preferred method.
2. Production Volume
Your production volume plays a significant role in determining which method to choose:
Low to Medium Volume: For projects with lower production volumes, CNC machining may be more cost-effective, especially when creating prototypes or limited runs. It allows for quick changes and adjustments without significant tooling costs.
High Volume: If you’re producing large quantities of parts, aluminum alloy casting can be more efficient. Once the mold is created, casting can quickly produce many identical parts, reducing per-unit costs significantly.
3. Material Considerations
Both methods utilize aluminum alloys, but the characteristics of the finished parts may differ:
Casting: Aluminum alloy casting allows for the production of parts with excellent fluidity and can incorporate a range of alloy compositions. Cast parts generally have good mechanical properties and can be optimized for specific applications.
Machining: CNC machining typically uses solid aluminum blocks, leading to denser and more durable components. Machined parts often have superior surface finishes and can achieve specific material properties that are advantageous for high-stress applications.
4. Cost Analysis
Cost is always a crucial factor in manufacturing decisions:
Casting Costs: While the initial cost of creating molds for aluminum casting can be high, the overall cost per unit decreases significantly with larger production runs. Additionally, casting can minimize material waste, further enhancing cost-effectiveness.
Machining Costs: CNC machining has lower initial costs, particularly for low-volume runs. However, the cost per unit may rise for larger quantities due to longer machining times and material waste.
5. Lead Time
The urgency of your project can also impact your choice:
CNC Machining: This method typically has shorter lead times, making it ideal for projects that require quick turnaround times or prototypes for testing.
Aluminum Alloy Casting: Although the initial setup time for mold creation may be longer, once established, casting can produce parts quickly for high-volume orders.
Choosing between aluminum alloy casting and CNC machining depends on several factors, including project requirements, production volume, material considerations, cost analysis, and lead time. By carefully evaluating these aspects, you can select the manufacturing method that best aligns with your project goals.
Whether you opt for the precision of CNC machining or the efficiency of aluminum alloy casting, understanding the strengths of each process will lead to successful outcomes in your manufacturing endeavors.
https://www.prototypeshlh.com/