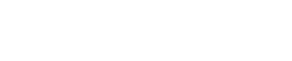
- info@prototypeshlh.com
- +86-133-9285-9203
- Room 2003, 20th Floor, Xingji Building, Shangde Road, Shajing Street, Bao'an District, Shenzhen
SERVICES
CNC Machining Service
Tight tolerances and finishing capabilities, as fast as 2 days.
Vacuum Casting Service
Production quality parts without the tooling investment.
Sheet Metal Fabrication
Experience the versatility 6 cost efficiency withflexible application options.
Die Casting Service
Create high quality custom mechanicals withprecision and accuracy.
Injection Molding Service
Production-grade steel tooling, as fast as weeks.
Popular Services
Injection Molding Service
A faster, easier way to order high-quality injection molded parts that accelerates iteration, testing, and scaled production. Upload your designs for DFM feedback and pricing in 24 hours.
3D Printing Service
Our 3D printing solutions cater to personalised needs with a diverse range of materials and colour options, including SLA, SLS, FDM, Projet, DMLS, and MJF printing services.
Surface Finishing
The easiest way to source your custom parts, with 15+ surface finishing options.
Design Guide
In-depth design guides full of best practices for all of HLH's manufacturing processes.
Case Studies
Success stories from innovativecompanies using HLH.
Blog
lndustry trends, company news andproduct updates.
Featured Posts
Aerospace & UAV
HLH is your 3D manufacturing partner from prototype to large scale production.
Consumer Products
New Product Introduction Solutions for Consumer Products.
Automotive
New Product Introduction Solutions for Automotive.
Industrial Machinery
The main purpose of industrial prototyping is to take the product from drawings into the real world.
Robotics & Automation
Need some assistance bringing your robotic device or parts from the sketch-board to reality?
Communications
We understand the demands and ever changing landscape of the communications industry.
Product Development
Industrial design and engineering consultancies are some of the most innovate and creative enterprises on the planet.
Vacuum injection molding is a manufacturing process that combines vacuum technology with traditional injection molding to produce high-quality plastic parts. It is widely used in prototyping and low-volume production due to its ability to create detailed, precise, and bubble-free components. This article explores the process, benefits, and the types of applications where vacuum injection molding is most suitable.
Vacuum injection molding utilizes a vacuum chamber to remove air and ensure even material distribution during the molding process. This method minimizes defects such as air bubbles and inconsistencies, resulting in smoother and more accurate final products.
(HLH Injection Modling Machine)
The process typically involves the following steps:
1. Mold Creation: A high-quality mold is created, often from aluminum or steel, designed to accommodate the desired part geometry.
2. Material Preparation: The raw materials, usually thermoplastic resins or silicone, are prepared for injection.
3. Resin Injection: Resin is injected into the mold under vacuum pressure, ensuring it thoroughly impregnates the fiber reinforcement.
4. Cooling and Curing: Once the mold is filled, the material is allowed to cool and cure, solidifying into the final part.
5. Demolding: After the part has cooled, the mold is opened, and the finished product is removed.
Vacuum injection molding offers several benefits, including:
1. High Strength-to-Weight Ratio: Produces lightweight yet strong components.
2. Improved Quality: The vacuum environment minimizes air entrapment, leading to parts with superior surface finishes and mechanical properties.
3. Complex Geometries: This method is particularly suited for producing intricate designs and thin-walled components that may be challenging with standard injection molding.
4. Reduced Waste: The precise control over material flow and elimination of air pockets leads to less scrap and waste material.
Vacuum injection molding is well-suited for a variety of applications and products, particularly in industries where high-quality and precision components are essential. Here are some examples of products that benefit from this method:
1. Automotive Parts: Components such as dashboards, housings, and decorative trims can be efficiently produced using vacuum injection molding, offering both durability and aesthetic appeal.
2. Medical Devices: The healthcare industry often requires parts that meet strict quality and safety standards. Vacuum injection molding can produce complex shapes for medical devices, ensuring precision and reliability.
3. Consumer Electronics: Casings and enclosures for electronic devices can be manufactured with fine details and excellent surface finishes, making them ideal for consumer products.
4. Aerospace Components: Parts for the aerospace industry, which often require lightweight and high-strength materials, can benefit from the unique properties achieved through vacuum injection molding.
5. Prototypes and Low-Volume Production: Vacuum injection molding is also a valuable method for creating prototypes or low-volume production runs, allowing designers to test their products before committing to larger-scale manufacturing.
Vacuum injection molding is an advanced manufacturing technique that provides significant advantages for producing high-quality components with complex geometries. Its ability to eliminate air pockets, improve surface finishes, and reduce waste makes it an excellent choice for a variety of applications, including automotive parts, medical devices, consumer electronics, aerospace components, and prototypes.
By understanding the benefits and suitable products for vacuum injection molding, businesses can leverage this technology to enhance their production capabilities and meet the demands of their industries.